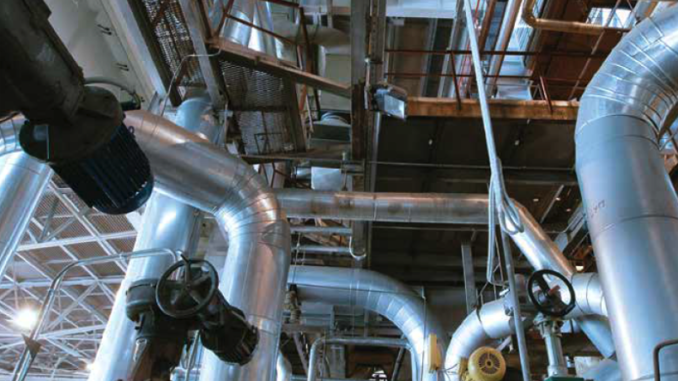
Contractors express concern over NEBC 2015 changes
by / Jessica Kirby
LAST YEAR marked the implementation of changes to the National Energy Code for Buildings (2015) that called for increases in insulation thickness on duct and piping by as much as 50 per cent in certain applications. Despite the changes’ potential to increase energy conservation and contractors’ profit margins, the industry is experiencing some pushback.
Steve Clayman, director of energy initiatives for the Thermal Insulation Association of Canada (TIAC), was part of the Pipe and Duct Insulation task group focused on lending input to the final draft.
From a manufacturer’s perspective, he says, thicker insulation means more insulation out the door and the impact is already being felt, particularly distributors because their product mix inventory is changing.
“They are having to bring in thicker insulation than in the past, and NECB 2015 is going to kick that up a bit over the next several years,” said Clayman.
While some contractors are indifferent or in agreement with the changes, others are feeling pressured by resulting industry adaptations. The changes say specified thickness must be the installed thickness, which isn’t a problem when it comes to rigid insulation because an inch and a half is an inch and a half. Flexible or blanket insulation cause problems, however, when it is pulled tight around the duct, mainly for aesthetic reasons.
“At the middle of the flat surface, whether it is vertical or horizontal, you might get the full thickness but as it gets closer to the edge, when it turns the corner the thickness is reduced quite a bit,” said Clayman.
The manufacturers state two R-values on the packaging: out of the package and installed, which shows the installed R-value allowing for 25 per cent compression.
“Typically, if a specification today was two inches and assuming the contractor buys two inches, when the contractor installed it, it would average an inch and half or less,” said Clayman. “The intent of the specifications is that the R-value drives the thickness. If you reduce the thickness on the application, you are reducing insulation value and there is wasted energy.”
Contractors who see the change in a positive light understand the changes boost a project’s bottom line, are good for the environment, and help create sustainable buildings. “From a profit perspective, if three inches of insulation costs a dollar and two inches costs 75 cents, the profit margin should, theoretically, put more money in their pockets because they are installing more insulation,” said Clayman.
The pushback, he adds, relates largely to a general resistance to change and a lack of clarity around the outward implications of the new code.
“We’ve never done it that way, there’s never enough room around the duct to accommodate increased thickness, more thickness is going to cost more money—there are many ideas out there,” said Clayman. “But the purpose of the code is to level the playing field. When you tell all the contractors competing on a specific project that this is the minimum requirement, that is what they have to bid on and install, or face sanctions.”
The competitive nature of the business has “kicked up a couple of notches,” said Clayman, since contractors have to buy a more costly product. “It is the right thing to do given global warming and CO2 in the atmosphere,” he said. “It makes long-term economic sense and contractors will have to deal with it.”
The changes have implications beyond economics. Duct and piping will require more space, which will require attention from mechanical engineers and contractors. While this may increase the total cost of a building, Clayman said this is just one example of the green movement’s impact on construction. “LEED, for instance, has added costs,” said Clayman, “but the costs are justified based on net results, which are saving energy.”
Contractors don’t often enough look at the positive side of change, he adds. “Because it’s thicker, you don’t get as much on the roll so you are handling more product and sometimes need extra people.
“Things like that have to be worked through in order for contractors to accept those changes.”
Another important change affects the process of insulating over a support. Any place insulation goes over a support bracket, such as an L-bracket used to support rectangular duct, the insulation is typically cut out so the visual impression is totally flat. Under the new code, the insulation can no longer be cut out and must instead be built up around supports to maintain the thickness integrity throughout the application.
“Where you have more mass in steel supports, valves, or elbows, the amount of steel emits more heat and if it isn’t covered to full thickness there will be heat loss at that point,” said Clayman. “And the pushback is, it is going to look patched up or terrible, it will cost more, it will take more labour to run the insulation over. Yes, but there is still heat loss we have to factor in, and here is the legislated away to deal with that.”
Non-compliance could have serious implications for building owners that will eventually trickle down to contractors. As part of energy conservation and building modelling in almost every jurisdiction, energy efficiency must be stated in a building proposal any time a permit is issued. If contractors make unauthorized changes, those changes will affect energy consumption and show up on the building’s post-occupancy audit.
“Building owners share energy consumption expectations with tenants who expect a certain level of efficiency,” said Clayman. “If a year after occupation the building isn’t performing, the owner has a major problem and he is going to want to know the source. LEED buildings also have stricter compliance requirements during construction.”
If a contractor is asked to install insulation below the requirement, he or she should write a letter to the specifier stating the discrepancy and asking for a revision or for the building plan to make up the energy loss in some other way. “And if he is told to make it work and stop bothering the specifier, at least he has that documentation to protect him later if things go awry,” said Clayman.
People within the TIAC organization are knowledgeable and could serve, if requested, as an excellent resource on the interpretation of the specification, what should be done, rationale, and the business case for doing it correctly, said Clayman.
He also points to support in municipalities taking the lead in energy efficiency—Vancouver, for instance, has beefed up enforcement requirements making building code inspectors (typically on the lookout for fire and safety compliance) responsible for ensuring buildings meet energy efficiency requirements. Calgary is moving towards this level of inspection, with Edmonton likely to follow. Toronto and Halifax and well as cities in Manitoba are also studying how to implement these changes.
Construction associations and local regulatory boards are in a position to ensure a smooth transition into the new requirements with plenty of lead time on announcing changes and by hosting outreach programs to answer questions and ease the process.
“In Vancouver, before all this passed, they made presentations to the Mechanical Contractors Association (MCA) members and other stakeholders to get buy-in,” said Clayman. “Rather than sit in Vancouver and say, ‘This is way it is going to be,’ they chose to reach out and explain the rationale for enhanced building code inspections. Vancouver officials were clear in explaining what non-compliance sanctions would look like;
not pretty.”
To find out more, please visit www.tiac.ca