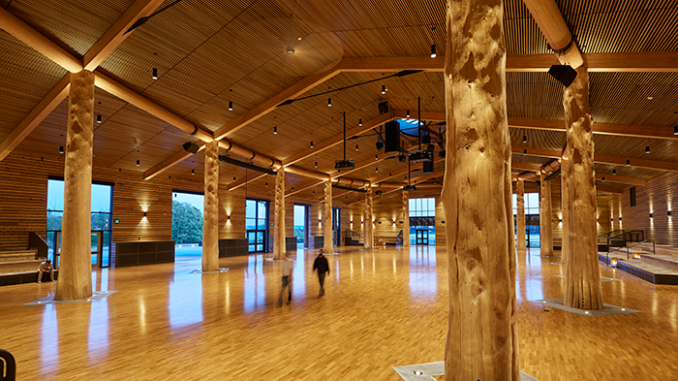
By / Jessica Kirby • Photos courtesy of TGB Architects and Johansen Mechanical Inc.
“It is important that we return to the tradition of gathering to revitalize our tribal values and integrate them into our emerging present-day culture. An increasing percentage of our tribal community are youth. Our gatherings need to help them to know our traditions and customs to help them into the future. We must balance between the old and the new … We must balance between what is meaningful and what is useful.”
—Tulalip Tribes
Location: Tulalip, WA
Project size: 61,000 square feet
Owner: Tulalip Tribes
Architect: TGB Architects
Sheet Metal Contractor: Johansen Mechanical
Tulalip Gathering Hall in Tulalip, Washington, is a multi-use facility carefully and thoughtfully designed to accommodate up to 1,500 tribal members for such activities as General Counsel, Pow Wows, meals, funerals, and other gatherings. It is sited on Tulalip Bay—the historic and cultural center of the Tulalip tribes—offering a sacred connection to the land and stunning views of Puget Sound.
According to TGB Architects, architect for the project, the form and materials of the building are simple and traditional—the ancient wisdom of tribal peoples draws them to gather in a circle, which allows them to both listen to a speaker and see the faces of the other listeners, helping them find the way to consensus and agreement.
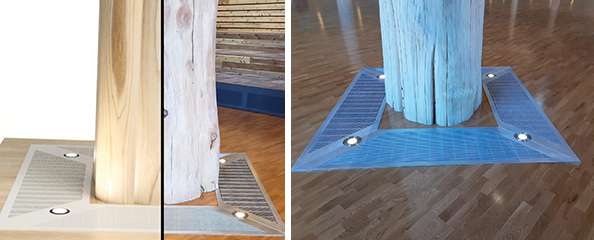
“Large supporting cedar columns in the main gathering space are arranged in a gentle curve to encourage a circling arrangement of gathering,” says TGB Architects. “This enclosing shape also references the shape of a canoe, which is an important artifact of travel for the Coast Salish People.”
The 12 cedar columns are finished like mighty trees that fit perfectly with the warm, interior wood finishes in the space. These include a high ceiling, polished wooden floor, extensive bleacher seating, and intricate wood working detail. But the columns are more than aesthetically pleasing. The base of each hosts a large custom floor grille, and supply air is served from basement ducts into a sheet metal plenum below the grilles. Air is then expelled around the perimeter of each pillar through the floor grilles.
The project was a unique undertaking for Johansen Mechanical Inc. (JMI), which had never installed an underfloor system in this type of application. “The below floor system achieved the look that the owner and architect wanted,” says Keith Johansen, president of JMI. “There is no exposed ductwork in the space, which provides a clean, streamlined aesthetic.”
JMI installed the entire mechanical system, which included 11 air handling units totalling 135 tons. When it came time to work on the floor grilles, Johansen’s site team quickly realized that the factory product specified lacked some important elements. Their ability to stand up to foot traffic was questionable, which may have led to warranty issues down the road. The grilles did not come factory built in a standard size, which meant they would have required supplemental structural components to be installed from underneath.
“It was a challenge to find a sufficient product and one that we felt comfortable with,” Johansen says. “We do custom metal fabrication ourselves, and we know what level of quality the grilles required. So, we provided an alternate solution.”
The in-house architectural metals group at JMI devised a concept for a custom grille. The project required 48 individual sections, and they needed a 5” circular shape built into each corner to accept lights.
Dan Moore, custom metals project manager, drew the mock-up using 3D imaging, which allowed rotational views of each side of each section and how the sections would fit together and incorporate the openings.
“The pieces match up on the flange end, each coming together at the corners to make a circular shape where lights fit in and shine upwards, “Johansen says.
Each grille section was engineered from aluminum bar grating to be both durable and removable for service and maintenance, and to be able to access the lights and plenum below. Sections had to be cut and welded to size, which also incorporated the required structural integrity. “It was down to the wire, so we quickly had to create the mock-up and pitch it in a GoTo meeting set up by BNBuilders, the general contractor,” Johansen says. “BNB was great to work with. We got approval from the architect to build a physical mock-up and present it at the job site. Once that was approved, we got the green light to do the balance and our shop came through in building them.”
“Overall, this was a great team effort,” Johansen adds. “When we faced challenges with the grilles, Dan did the concept drawing and 3D mock-up and ran the GoTo meeting. Between Mark Nosbusch, field superintendent; Justin McGovern, field foreman; and Bill Allen, shop foreman, coordination between the shop and field was flawless.”
Johansen’s work also included a full kitchen and two type 1 hoods with welded grease duct. The company provided upfront BIM coordination—working with Pacific BIM Services— and realized that in some places the truss space was too tight to accommodate the new ducts.
“This was another challenge, as BIM pointed out the issues with the truss layout and not fitting the ductwork in properly,” Johansen says. “We had to get them to change some of the trusses to allow the new ductwork to fit.”
Another important partnership involved K&R Indoor Air Quality, a small tribal company with which JMI has teamed up on other Tulalip projects. “K&R helped out on the project management and tribal relations aspect,” Johansen says. “We are very grateful for our long-term working relationship with Bob Lane and K & R”.
Despite the site closing temporarily in mid-March due to COVID, the project completed in May.
“We are really happy with how it turned out,” Johansen says. “The building is extremely important to the Tulalip Tribes, and we are proud to have been involved with this unique project.”
Ryan Duckworth, BNBuilders project manager, says the team at Johansen was terrific to work with and consistently met the project standard for setting and keeping durations and milestone dates, and pushing other trades to stay on track.
“The knowledge their site supervision provided helped quickly and effectively resolve issues with the design and work through the challenges every job faces between some difficult contractors, procurement delays, and scope gaps,” he says.
“The team’s willingness to fill those gaps with the in-house specialty metals work has helped keep us on track here at the end, and I appreciate Johansen’s understanding of budget constraints and efforts to help control those costs.” ▪