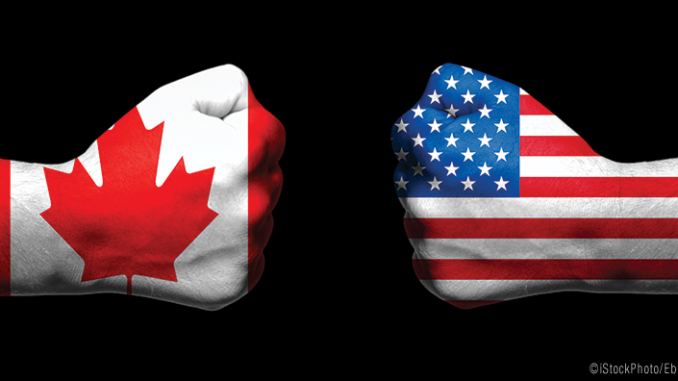
SMACNA-BC and the construction industry weigh in on the tariff landscape
By / Robin Brunet
The only sure thing in these tariff-driven times is that United States president Donald Trump is a master at fomenting uncertainty. His actions against Canada have caused speculation that everything from a more equitable realignment of free trade to an outright global depression is forthcoming.
Ever since Washington imposed a 25 percent tariff on imports from Canada and Mexico on March 4, the Canadian construction industry joined the angry chorus of voices to express what may lie in store for them. “These measures are likely to impact not only the ability of construction operators to meet their project requirements, but also the supply chains that the Canadian industries rely on,” stated the Canadian Construction Association. “This limits the industry’s ability to combat the housing crisis, it slows down its ability to build critical infrastructure, and so much more.”
Of equal concern is the prospect of retaliatory Canadian tariffs on American construction materials brought into this country (we import some $3.5 billion in glass and glass products, for starters). Canadian Home Builders’ Association CEO Kevin Lee believes an emphasis should be placed “on avoiding tariffs on construction products and materials, unless other domestic or import solutions can be easily found for comparable prices.”
For its part, the Vancouver-based BTY Group examined six categories of construction materials at risk of the tariffs and concluded that construction costs could go up by between four and six percent. It also postulated that if potential retaliatory tariffs were taken into account and remained in effect for an extended period, a disinflationary trend would occur as demand falls and activity slows (in which case costs would go down).
As for BTY’s ranking of at-risk materials, lumber is considered a high risk, as are mechanical and electrical systems. In the medium risk category is rebar, due to some reinforcing steel production in Canada and the ability of bigger firms that buy supply from the United States to pivot to sources at home. BTY considers concrete to be steady and glazing to be a low risk.
But the degree to which the construction sector will suffer still remains a mystery, and Jeremy Hallman, executive director at SMACNA-BC, is unwilling to forecast anything with any degree of authority. “I’m tempted to say that the sheet metal sector will be less affected by the tariffs than other construction sectors, for the simple reason a lot of our members make their own products,” he says. “However, the price of everything from screws and bolts to insulation and sealers will likely go up, and I doubt any of us will truly grasp the impact until later this year.”
Hallman speculates that some Canadian companies may benefit, particularly if they specialize in specific sectors, such as the manufacture of commercial and industrial HVAC products.
But unfortunately, more common are the complaints Hallman is hearing from colleagues. “One SMACNA contract member who imports material from the United States to create a finished product up here that in turn is shipped back to America told me that 45 percent of his work goes stateside, and he’s extremely concerned about his bottom line,” he says.
At least one SMACNA associate member informed Hallman that the crunch has already begun. “He said he ordered a fan from the United States and that it came with a small premium, which he was able to absorb,” Hallman says. “But when that fan reached the Canadian border, customs slapped a 25 percent counter tariff on it. The member told me, ‘I can’t ask my customers to pay the extra, but I don’t think I can absorb the cost either, if this keeps up.’”
Consultancy CliftonLarsonAllen points out the catch-22 such people are faced with. “Absorbing the costs can squeeze profit margins and limit the ability to invest in new projects or hire additional workers,” it reports. “Passing the costs on to clients can make new construction projects less attractive, potentially reducing the demand for new buildings and infrastructure.”
One Vancouver-based supplier of condensing boilers and water heaters told Sheet Metal Journal on condition of anonymity, “In this environment, planning becomes extremely hard to do, and for many companies that have established set project prices from bidding that occurred prior to the tariffs being announced, it will be challenging to get the job done.”
Despite all the turmoil, Hallman is reluctant to panic. “As horrendous as the covid years were, they took online meetings to new levels and saved a lot of travel time and money, ditto for transactions such as electronic payment. So, I’m hoping we can look back on tariffs and say that they bolstered our self-sufficiency and resilience.”
Hallman is not alone in seeing a silver lining. Sean Strickland, executive director of Canada’s Building Trades Unions, says, “Canada is rich with talented workers and natural resources. Through strategic investments in infrastructure that opens new trade routes, enhances transportation networks, and enables access to international markets, Canada can diversify our trade partnerships and maximize the value derived from our goods and resources—while investing in economic growth that delivers high-paying jobs for Canadian workers.” ■