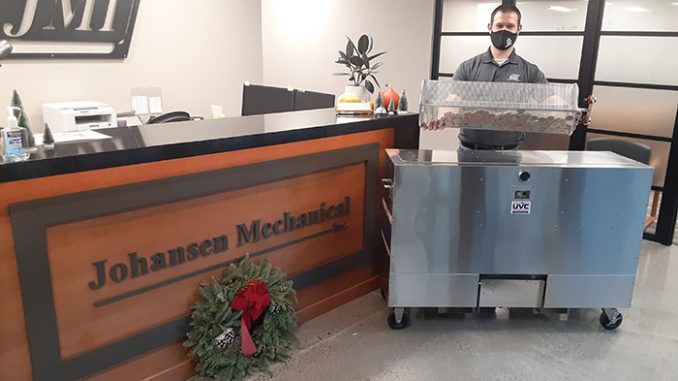
By / Jessica Kirby • Photos courtesy of Johansen Mechanical Inc.
In April, a shortage of PPE for health care professionals inspired the owners and workforce at Johansen Mechanical, Inc. (JMI) in Monroe, Washington, to take action. JMI owners Keith Johansen and Derek Holm, along with project manager Daniel Moore, put their heads together to develop the Hands-Free UVC disinfecting chamber, a machine that uses UV light to kill COVID-19 and any virus on any surface.
“We’ve encountered many challenges in the condensed development period of our machines, but we’ve also kept the goal of serving our communities in mind and pushed through to get us here today,” said Moore, who is a project manager in JMI’s architectural metals department, and designer of the Hands-Free UVC units. Daniel, a machinist by trade, has a background in custom metals and stainless, and crafted the idea for the design from the wiring and drawing to the fabrication.
Effective means to minimize infection is of paramount importance to limit spread, as viruses can be transmitted via aerosol and survive for days on surfaces outside the human body. Disinfection technology using UVC light is one of the most reliable and widely accepted methods of keeping surfaces clean without the use of chemical solutions.
UVC was identified more than 100 years ago as an effective means to disinfect and purify air, water, and surfaces. The way it works, ultraviolet light is defined in three wavelength groups, A, B, or C. The sun produces light, and we are exposed to the sunlight’s UVA and UVB rays. UVC does not make it through our atmosphere because it is blocked by the ozone layer. The germs, bacteria, and viruses creating most illnesses cannot resist the harmful effects of UVC, which makes them inactive.
Given today’s drive for cleaner, more crowd-friendly public spaces, UVC use in small spaces and by portable means is the subject of extensive research and development. In Seattle, the Space Needle has invested $1 million into UVC sanitizing technology, including UVC body scanners at the gate that look like airport metal detectors and UVC-purified air systems. Boeing release a UVC wand at the end of 2020 that will be used to disinfect all of its aircraft surfaces from door handles to instrumentation.
In the Hands-Free UVC units, germicidal lamps use the optimal UVC wavelength to destroy illness-causing germs, including viruses and bacteria. Surface exposure to UVC is capable of inactivating microorganisms, such as germs, bacterial, and viruses. With UVC technology being a naturally occurring process, it becomes an effective environmentally friendly and chemical-free process to inactivate these pathogens and reduce their transmission.
“Hundreds of hours have been dedicated to this project to make sure the units are safe for users,” Daniel says. “The foot controls keep our users from passing germs from one user to the next. Multiple safety interlocks prevent exposure to the 254nm UVC light, and the electronics, mechanical, and photo-biological testing have all been inspected by the international testing service ETL.
Applications for two different unit types include offices, manufacturing, medical, dental, assisted care facilities, schools, casinos, and many more. The HFUVC-100 features a smaller, compact design for small spaces. It has a 2.5 ft3 chamber volume and a 29mL/cm2 90-second average UVC output, and it is ETL certified for photobiologic, electric, and mechanical. It is best suited for disinfecting personal protective equipment, electronics, accessories, writing utensils, books, and other multiple objects.
The larger HFUVC-200-AP unit was designed in response to a private school looking for a machine that could disinfect as many as four basketballs at once. This larger, mobile unit has a 4 ft3 chamber volume, a 90-second average UVC output of 50mJ/cm2, and an air processing mode with a 15×20 foot room capacity. It is essentially a larger version of the original model and so disinfects similar items in addition to sports equipment, fine arts supplies, tools and measuring equipment, keys, computers, and lab equipment.
“Our focus is to help and serve our communities by providing high quality, safe, and reliable disinfecting units to support the public and private sectors’ need for long term disinfecting,” says Holm. “Our customers will now have protection against present and future pathogen outbreaks while keeping our environment safe from harsh cleaners and chemicals.”
The latest development is a tumbler accessory in the larger unit, which allows for disinfecting small, high volume items like dice and casino chips. So far, one local casino has purchased a unit, and many more have expressed interest. Two local private schools have also purchased units, as well as a sanitation company in Thunder Bay, ON, Canada.
“You would be amazed as to how versatile the units are with so many different uses,” Holm adds. “Every time we speak with someone about this project, they provide more uses we haven’t even thought of yet.”
Bill Allen, shop superintendent with JMI, says the company’s ability to craft the units, which require exact dimensions and tolerances, comes down to the company’s innovative leadership and its skilled and experienced union workforce.
“A lot of the time, our custom metals department has to take the architect’s vision and convert it to a masterpiece,” he says. “This process requires extensive communication between the architects, project management, and our fabricators.”
The components are laser cut so there is no drilling, just forming, assembling, and everything is pop riveted together. In the early stages of any project, the fabricators are involved with the project management team to plan ahead to avoid potential fabrication and installation challenges. This planning streamlines the entire process and helps JMI ensure it beats the targeted schedule, margins, and customer satisfaction.
“The fabricators in our custom metals division are a select group of the best fabricators in the industry with attention to detail that sets them apart from the rest,” Allen says. “It is a mindset that is required to know that what you are working on can’t just be close enough; it has to be right. We are fortunate to have a team that operates under this mentality and is able to exceed these high expectations efficiently.”
Prototyping is one of the shop’s specialties, he says, which requires good communication and planning with the customer, project management, and the fabricators.
“Documentation of the process to incorporate any changes throughout prototyping is also very important in order to make the production units turn out perfect,” Allen says. “JMI has all the aspects of equipment, labor, and expertise required to form, machine, and weld a product that we are proud to make here in Washington.”
JMI recently made an investment in a new fiber laser cutting machine to enhance the niche market work the company performs.
Building locally is important to Johansen and the rest of the team.“This project ties into our corporate goal of supporting and making a difference in our local community,” he says. “We are able to make a positive difference during this pandemic in the United States, Canada, and hopefully, globally. We are proud of Daniel’s innovation and all his extra effort to make this project successful.” ▪