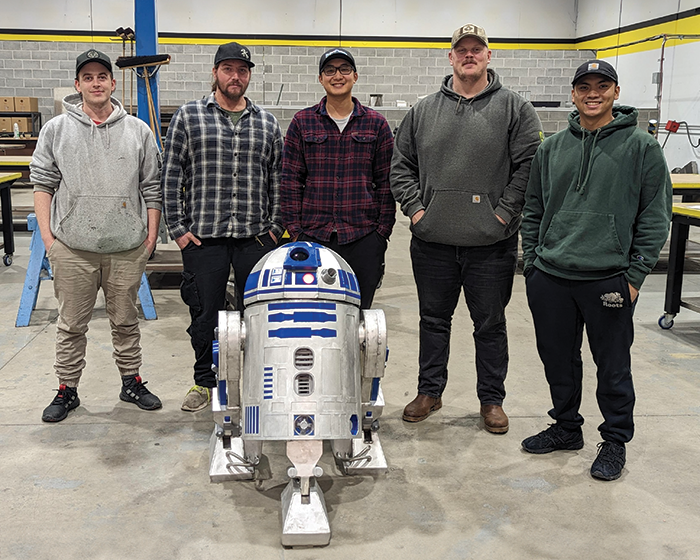
By Jessica Kirby • Photos by Colin Nam
Five apprentices at the Sheet Metal Workers’ Training Centre (SMWTC) have mastered the Forces of creativity, problem-solving, and hard work by creating a life-size, working R2D2 model—complete with a sound board and spinning head—for their fourth-year project.
“We encourage creativity at the training centre, and in fourth year, apprentices traditionally build a generic tin man as a group project,” says Jake Leblanc, head instructor at SMWTC. “Most groups customize their tin man and pick a theme—we have had Batman, a golfer, a German guy with lederhosen, Bender the Robot, a devil Bender the Robot, Santa Claus, and many more.”
In his third year, Colin Nam made the character Bender from Futurama, so in fourth year, instructor Matt Brown approached him with a challenge: one-up the Bender project. After brainstorming a few ideas, the two decided an R2D2 replica model would be very challenging but possible. Nam assembled a crew.
He called on classmates Troy Martins, Ethan Picanca-Nyberg, Mitch Guillermo, and Aaron Arnal to help fabricate and assemble the pieces of this complex puzzle.
But first, there was research to be done. Nam joined a forum dedicated to building replica R2D2 models, where he found the correct sizes and proportions. He used these to make AutoCAD drawings of R2D2 and started to dissect how to fabricate and assemble each piece.
“Next, I created detailed layout drawings of the pieces required for each part,” he says. “I gave these drawings to the rest of the crew to start shearing, braking, and forming.”
Ethan and Mitch—chosen for their high attention to detail and fast hand layout skills—sheared and formed most of the pieces.
“They came out extremely well, which made it easy for Aaron to weld them together,” Nam says. “Aaron was fast and efficient, and I felt like our team was able to co-operate well together with this assembly line. We all spent extra time after class and some time during our lunch breaks to complete this project.”
While most of the pieces are similar to HVAC fittings, thus fairly simple to make, the head was an entirely different matter. It took a few hours in AutoCAD to figure out how the team was going to make the shallow dome.
“I decided on 12 tapered pie pieces that we would roll up to make them meet in the middle,” Nam says. “I’ll be honest—I had no idea if it was going to work.”
He sent the DXF file from AutoCAD to Mitch who, luckily, was able to cut the pieces on a laser table at his shop. “I don’t think we would have been able to do it as accurately if we had to cut these by hand,” Nam says. “And it saved us a whole day’s work.”
Troy, the most experienced with rolling pipe and pieces to match precise measurements and diameters, had the daunting task of rolling up the pie pieces for the head. Each piece had to be rolled perfectly, the same way, to the right diameter. “Because they taper, we had to reduce the tension of the rolls near the tip of each piece,” Nam says. “This means changing the rolls for each piece and replicating the process precisely. Troy did an excellent job with it.”
Originally intended for static display, R2D2 soon became much more. Nam wanted to try adding lights, sounds, and moving parts, so he added three extra components that would later lead to a bigger challenge than expected.
In the quest to make R2D2’s head spin, Nam discovered that a “Lazy Susan” bearing would be the perfect size to fit the body’s diameter. In AutoCAD, he designed an 18” diameter ring that had a smaller gear on the inside with matching teeth. “This was intended for a small motor to be mounted to the inside of the body,” Nam says. “The small gear would be attached to the motor and the ring would sit on the Lazy Susan and spin the head as the gear turns.”
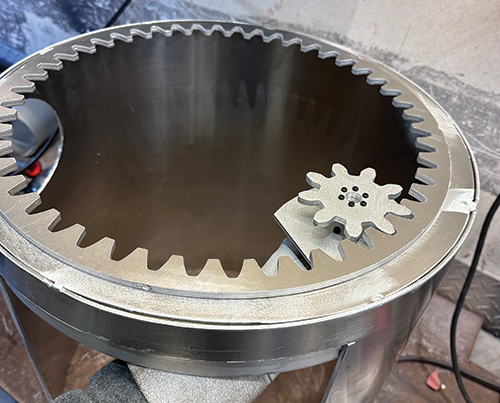
Nam started to model parts after school on his home 3D printer. While most of R2D2 is made from aluminum, these parts added some intricate details that would otherwise be impossible to make within the given timeframe. On the forum, he found soundboard ideas, basic wiring diagrams, and a lighting kit, which he ordered.
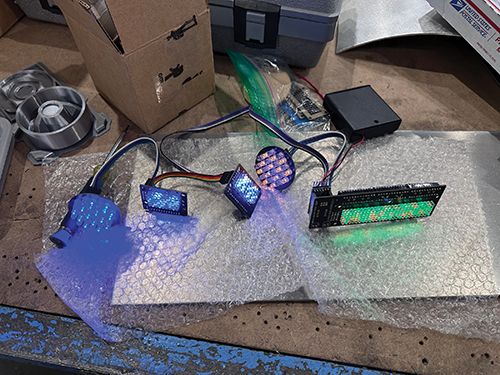
These were the most challenging part of the build, since the team had no experience with wiring motors, motor controllers, or sound boards. R2D2 is powered by a 12V drill battery connected to an Arduino, which is the mother board and “brains” that transmit data from a button input to a soundboard, motor, and speaker.
“I have never coded before, but I had to learn how in order to connect all these devices together,” Nam says. “By the time we got to this stage, I had four days to learn how to code and get all the motors and sounds synced up.”
After spending 8-12 hours over three days after school, Nam managed to bring R2D2 to life. “Press a button and the signal tells the motor to spin a certain direction for a specific amount of time while playing a sound,” Nam says. “There are six available sounds and each one does something a little bit different.”
R2D2 is basically split up into four main sections: head, body, and two legs. After each section was welded and the 3D printed parts were attached, the team managed to finally put it all together on the last available day they had in the shop, which was on the weekend outside of regular school hours.
“While I was working on the design and moving parts, I fully trusted in the guys to get all the pieces fabricated properly,” Nam says. “Everyone I chose to help with this project had a specific role, which helped us work together efficiently.”
Currently, R2D2 is at the training centre on display. Nam plans to take R2D2 home for an upgrade that will include motors and wheels in the feet and remote operation capabilities.
“I will eventually bring it back to the school so people can play around with it,” Nam says. “The long-term future for R2D2 is unknown but for now our team has decided that the intention is to inspire other students to make cool projects.” ■